The Alchemist’s Formula: A Beginner’s Guide to Ribbon Restoration Techniques
There’s a profound beauty in holding a piece of history in your hands. For those of us drawn to the world of antique typewriters, that beauty isn't just in the cast iron frame or the satisfying click of the keys. It’s in the ribbon. A faded, brittle ribbon is more than just a part; it’s a silent witness to untold stories, a tangible link to the hands that once crafted letters, poems, and manifestos. To restore a ribbon is, in a way, to resurrect a voice.
I remember my first ribbon restoration. It was a dull, brownish-grey thing from a 1920s Underwood. I’m ashamed to admit, my initial approach was…aggressive. I’d read a few scattered online tips – things about soaking in alcohol, careful drying – and dove in with reckless abandon. The result? A crumbly mess. It was a harsh lesson in patience and respect for these delicate artifacts. The experience taught me that restoration isn't about conquering; it's about gentle coaxing, about understanding the material and the processes that shaped it.
This isn't a quick fix, and it certainly isn't foolproof. Ribbon restoration is an art – a delicate dance between science and intuition. We’re not just dealing with ink; we're dealing with a complex mixture of pigments, binders, and carriers, often interwoven with materials like silk, linen, or even early forms of plastic film. The process requires observation, experimentation, and a healthy dose of humility. The subtle variations in material composition often speak volumes about the era they originate from; a deeper look at Deconstructing the Spine: Examining Ribbon Material and its Implied Legacy, reveals just how much information can be gleaned from the very fabric of these ribbons.
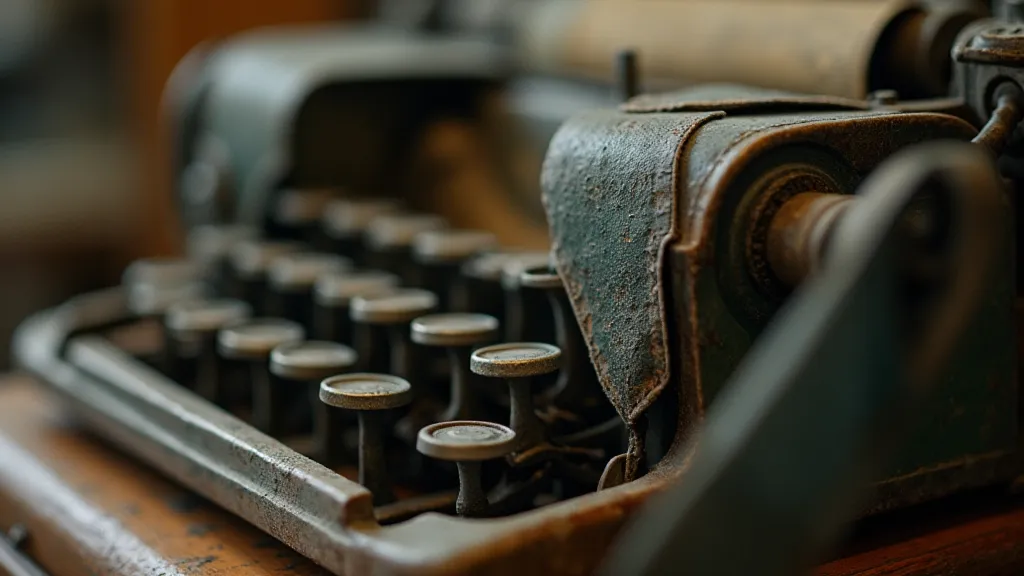
Understanding the Enemy: Ribbon Degradation
Before we can even contemplate restoration, we need to understand *why* ribbons degrade. The usual suspects include light exposure (UV radiation is a ribbon's worst enemy), oxidation (reaction with oxygen), and chemical breakdown of the binders. Heat and humidity exacerbate the process. The type of ink used also matters; early ribbons often used inks based on natural pigments that are far less stable than later synthetic dyes. A ribbon from a 1905 Royal will behave very differently than a ribbon from a 1950s IBM Selectric.
The colour of the ribbon is also a crucial identifier. While black was the standard for most of the early 20th century, other colours existed – crimson, purple, even green. These rarer colours are highly sought after by collectors and their condition often reflects their relative obscurity and handling. The stories these unusual colours tell are often captivating; understanding Beyond Black and White: Exploring Uncommon Ribbon Colors and Their Story unlocks a deeper appreciation for the artistry and historical context surrounding these vintage writing tools.
The Gentle Approach: Cleaning and Stabilization
The first step in restoration isn't aggressive cleaning; it's stabilization. We want to prevent further degradation. This begins with careful handling. Wear cotton gloves to avoid transferring oils from your hands. Store ribbons flat, in a dark, cool, and dry environment. Acid-free tissue paper is your friend – wrap the ribbon loosely to protect it from light and physical damage.
Cleaning is about removing surface contaminants – dust, dirt, and grime. The gentlest approach is often the best. A soft brush, like a goat hair paintbrush, can be used to carefully remove loose particles. For more stubborn grime, a slightly damp (distilled water only!) cloth can be used, but with extreme caution. Rub gently and dry immediately with another soft cloth. Avoid vigorous scrubbing; you’ll likely damage the ribbon further.
The Alcohol Bath: A Proceed with Caution Technique
The alcohol bath is a controversial topic. Some restorers swear by it, while others consider it a recipe for disaster. The theory is that alcohol can dissolve some of the surface impurities and rehydrate the ribbon, bringing back some of its lost flexibility. However, it can also dissolve the ink, leaving you with a faded ghost of what was once there.
If you choose to proceed, use 99% isopropyl alcohol, diluted with distilled water (a 1:1 ratio is a good starting point). Submerge the ribbon for a very short period – 15-30 seconds is often enough. Immediately remove and blot dry with a soft cloth. Monitor the ribbon *constantly* during the process. Any signs of ink bleeding should prompt you to terminate the bath immediately.
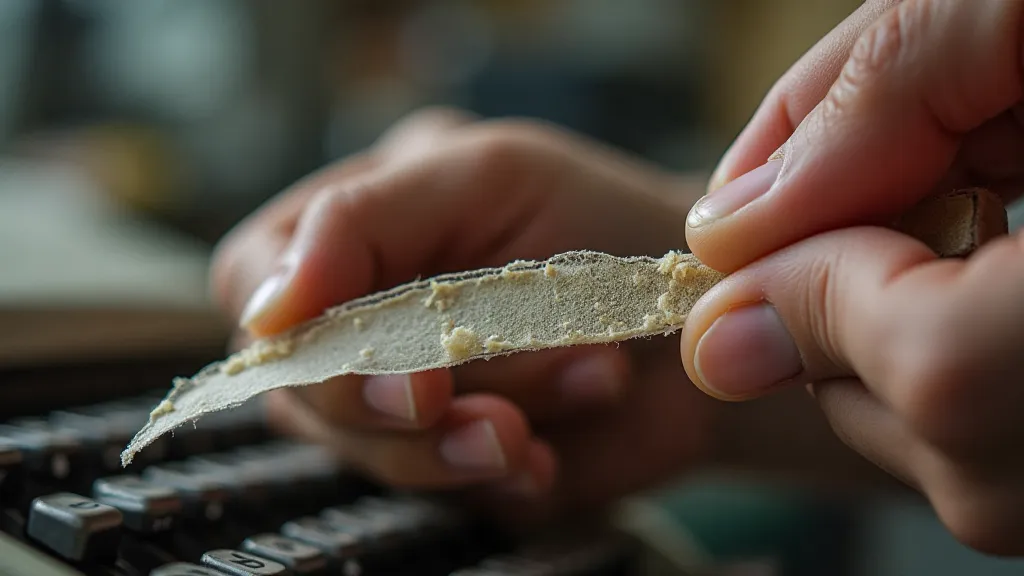
Rehydration and Flattening
Once the ribbon is clean and potentially stabilized, the next step is rehydration. This helps to restore some of its lost flexibility. Again, distilled water is your best friend. A barely damp cloth can be gently applied to the ribbon, followed by immediate drying. Avoid soaking the ribbon; a surface hydration is what we’re after.
Flattening a warped ribbon can be tricky. Placing it between sheets of acid-free paper and applying gentle weight (a few books will do) can help. Be patient; this process can take several days. Avoid using heat, as this can further damage the ribbon.
The Art of Identification: Color, Manufacturer & Typewriter Compatibility
Identifying a typewriter ribbon is a puzzle in itself. Ribbons rarely bear clear markings, especially early ones. However, clues can be found. The color, the fabric (silk, linen, plastic), and any faint markings (a small logo or manufacturer’s name) can provide valuable information. The typewriter the ribbon came from is, of course, the biggest clue. Different manufacturers used different ink formulations and ribbon fabrics, and certain typewriters were specifically designed to use certain types of ribbons.
Research is key. Online databases, typewriter manuals, and collector forums can be invaluable resources. Understanding the history of typewriter ribbon manufacturing helps tremendously. Early ribbons were often made by the typewriter manufacturers themselves (Underwood, Remington, Royal), while later ribbons were produced by specialist ribbon companies. The evolution of ribbon technology mirrors the wider evolution of the typewriter industry. Examining Resonance of the Machine: How Ribbon Spacing Reflects an Era’s Aesthetic reveals a fascinating connection between the physical characteristics of these ribbons and the design philosophies of their time.
Further investigation into manufacturers often requires a keen eye for detail, as markings are frequently subtle or completely absent. Even the spacing between characters, dictated by the ribbon’s width and the typewriter’s mechanics, provides a vital piece of the puzzle. Knowing how these elements interacted throughout the history of typewriter manufacturing can significantly enhance the identification process.
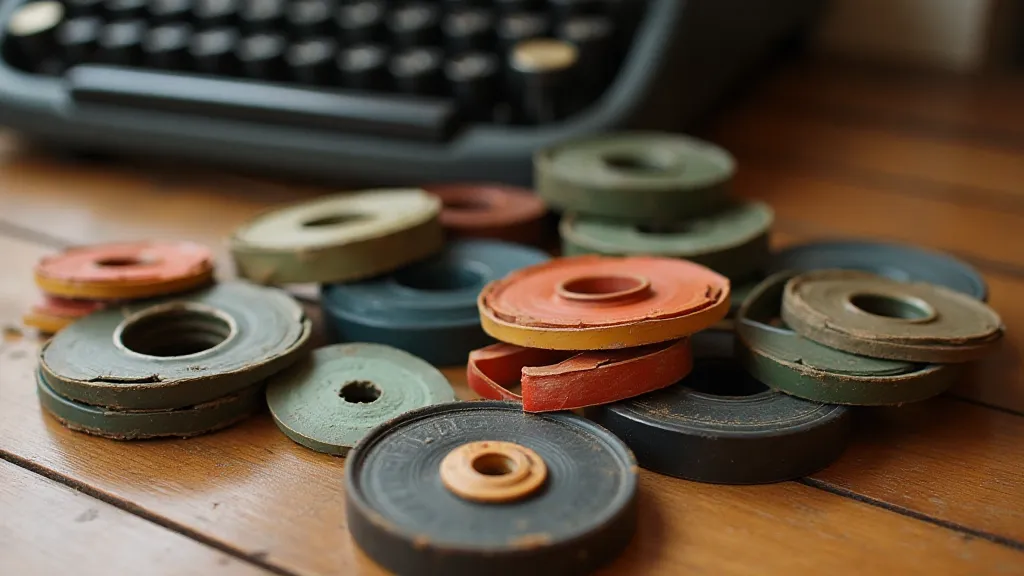
The Cartographer's Compass: Identifying Ribbon Origins
Tracing the origins of a ribbon is akin to following a cartographer's compass – a meticulous pursuit guided by subtle clues. The composition of the ribbon itself – the weave of the fabric, the consistency of the ink – are all key indicators. Analyzing these characteristics alongside any surviving markings, even partial or faded ones, can lead to a surprisingly detailed picture of the ribbon's history. Manufacturers often employed unique techniques, leaving behind telltale signs that can be identified by experienced collectors. Considering The Cartographer's Compass: Identifying Ribbon Manufacturers Through Subtle Details will help refine your detective skills in the world of vintage ribbons. These seemingly minor details often serve as invaluable fingerprints, connecting a ribbon to its maker and illuminating a piece of typewriter history.
Furthermore, the context in which the ribbon was found provides crucial information. Was it discovered within a specific typewriter model, or bundled with other typewriter accessories? These associations can offer hints about the ribbon’s intended use and potential manufacturer. The more one understands about the manufacturing processes and business practices of the early typewriter industry, the easier it becomes to decipher these clues. Early ribbons frequently served as silent ambassadors for their manufacturers, reflecting the quality and innovation that defined the era.
The Ongoing Quest: Gentle Reminders
Restoring antique typewriter ribbons is not about bringing them back to pristine condition; it’s about preserving what remains. It’s about appreciating the craftsmanship and the history embodied within these fragile artifacts. Each ribbon tells a story, and it's our responsibility to ensure that those stories continue to be heard.
Remember these key takeaways: Patience is paramount. Experimentation should be conducted with extreme caution. And always, always prioritize preservation over perfection. The goal is not to restore a ribbon to its former glory, but to stabilize it, allowing it to whisper its secrets for generations to come.