Chromatic Ghosts: Unearthing Lost Color Combinations in Ribbon Production
There’s a peculiar melancholy that settles over me when I hold an antique typewriter ribbon. It's more than just the brittle fragility of the material, the faint scent of ink and age clinging to it. It’s a sense of time slipping through my fingers, a tangible link to a world of meticulous craftsmanship and a palette of colors largely forgotten. We often focus on the machines themselves, the elegant curves of an Underwood or the robust mechanics of a Remington. But the ribbons, the vital arteries feeding those machines with their voice, hold their own secrets – whispers of a lost artistry in color production that often goes unnoticed.
My interest in these chromatic relics began with a simple restoration project. I was attempting to revive a 1920s Smith Corona, and the ribbon I’d initially sourced felt…wrong. It lacked the depth, the vibrancy of the faded impression on the machine’s original documentation. This initial disappointment sparked a deeper investigation. I started asking myself: What colors were truly available? Who was making them? And why are so many of these hues so scarce today?
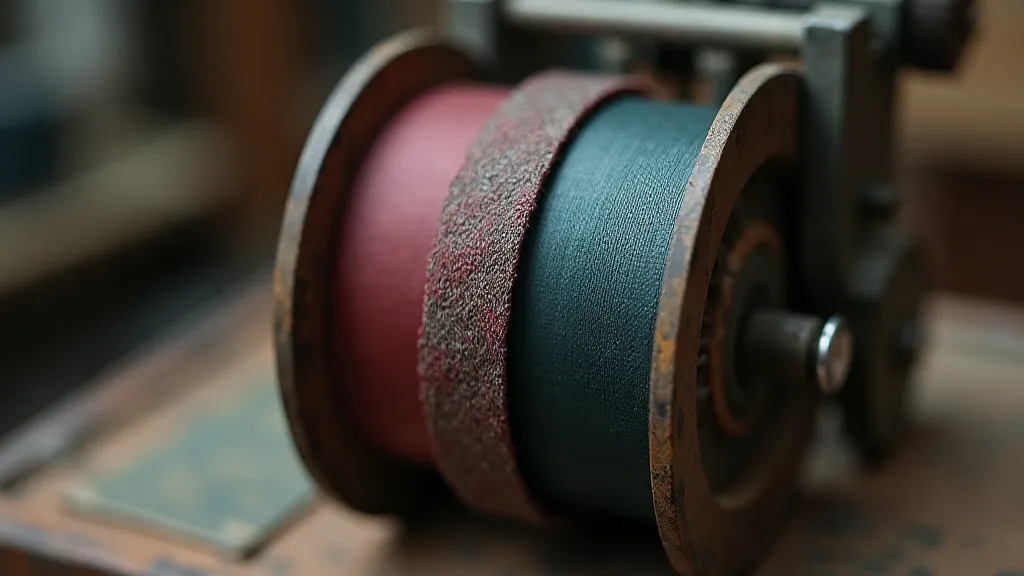
The Golden Age of Ribbon Manufacturing
The early 20th century witnessed a flourishing industry dedicated solely to the production of typewriter ribbons. Companies like Letchert & Abbott, Borden & Co., and Ideal Ribbon Company were titans in their own right, employing teams of chemists and dye masters who experimented tirelessly with color formulations. These weren’t just about producing black or red ribbons; they aimed for a spectrum of shades – deep purples, rich olives, delicate rose hues, even subtle shades of gray that mimicked photographic tones. The sheer variety is astounding, and truly speaks to a dedication to aesthetics often lost in modern manufacturing. It begs the question: how did these colour variations come to be? The process wasn’t just about mixing chemicals; it was a delicate balance of art and science.
The dyes themselves were derived from a wide range of sources, often utilizing natural pigments initially, and then gradually transitioning to synthetic compounds as chemistry advanced. The process wasn’t exact, and variations in raw materials and manufacturing techniques led to subtle, yet significant, differences in the final product. A “red” ribbon from one manufacturer might appear significantly different from the “red” ribbon produced by another, even when seemingly identical in description. These nuances in production methods often resulted in slight alterations of the final shade, making the search for exact replacements incredibly difficult. It wasn't always about producing "red," but creating *their* red.
The Disappearance of Subtle Hues
So, what happened to these captivating colors? Several factors contributed to their decline. The rise of cheaper, mass-produced ribbons, often focused on basic black and red, prioritized cost over aesthetics. Synthetic dyes, while initially promising a broader spectrum, proved unpredictable and difficult to consistently reproduce, leading manufacturers to revert to safer, more predictable options. Beyond the manufacturing changes, consumer preferences shifted. As typewriters became more ubiquitous, the desire for unique and expressive colors faded. The focus moved to functionality and durability, and the artistry inherent in ribbon production was deemed, unfortunately, expendable. Collectors began to forget the range of colours, and the knowledge regarding these colours was lost.
The standardization of production also contributed. To achieve a consistently predictable output, the nuances of older, more artistic processes were deliberately eliminated. The search for perfection in uniformity, however, ironically led to a loss of character and individuality. It’s a stark reminder that the relentless pursuit of standardization can sometimes erase the beauty found in imperfections. Understanding the intricacies of these processes and their impact on the final product is a pursuit not unlike the one described in a beginner’s guide to ribbon restoration techniques.
I remember finding a box of ribbons at an estate sale a few years ago. It was a chaotic jumble – brittle, dusty, and largely unidentifiable. Amidst the black and red, however, lay a few treasures: a ribbon described simply as “Lavender Gray.” It wasn’t a vibrant purple; it was a subtle, almost ghostly shade, possessing a quiet elegance that resonated deeply. Holding it, I felt like I was holding a fragment of a lost aesthetic – a reminder of a time when even the most utilitarian objects were imbued with a sense of beauty and intention.
Identifying Rare Combinations: A Detective's Work
Identifying antique typewriter ribbons isn't a straightforward process. Manufacturers’ markings are often faint, incomplete, or entirely absent. Color descriptions on original documentation are notoriously vague, relying on subjective terms like "slate," "olive drab," or "burnt sienna." It’s a detective's work, combining visual comparison, historical context, and a healthy dose of educated guesswork. Deciphering these descriptions requires not only a keen eye but also an understanding of the language used at the time – a language steeped in nuance and often quite poetic.
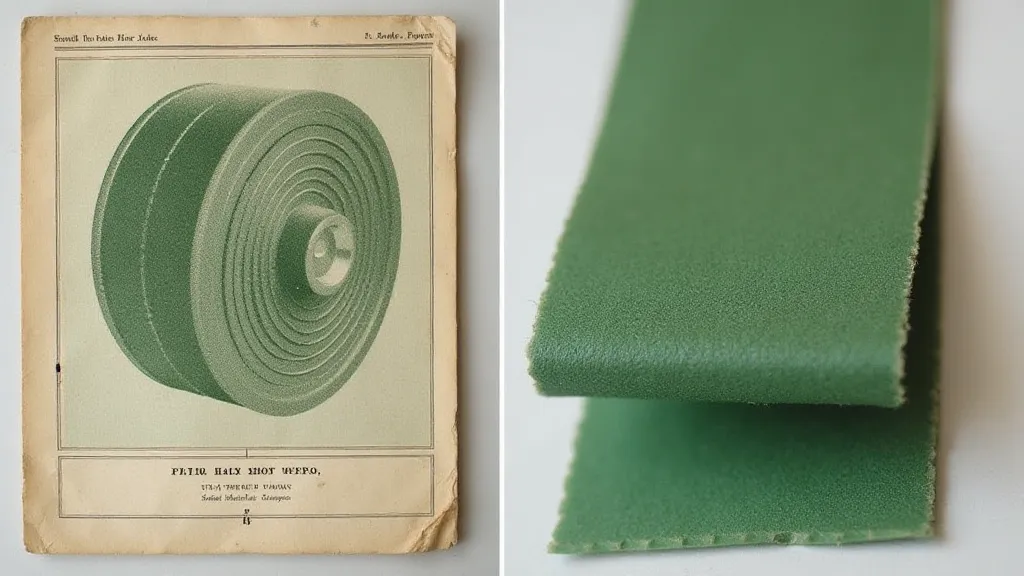
One useful technique is to compare ribbons to surviving advertisements and catalogs. These often provide clues about color names and intended applications. However, it's important to remember that color reproduction in these materials was often inaccurate, and what appears "olive green" in a catalog might be closer to "pea green" in reality. Another valuable resource is online forums and communities dedicated to typewriter collecting and restoration. Sharing observations and comparing notes with fellow enthusiasts can often lead to breakthroughs in identification. Examining the broader context of these artifacts often reveals deeper insights; it’s about understanding the aesthetics of an era, a quest not unlike that explored in deciphering hidden symbols on vintage ribbons.
Beyond Aesthetics: The Impact on Restoration
The scarcity of original ribbons isn’t just a concern for collectors; it has a significant impact on typewriter restoration. Using incorrect ribbon colors can drastically alter the character and value of a restored machine. A vibrant purple ribbon on a 1930s Underwood, for example, feels jarringly out of place, detracting from the machine's authenticity. The interplay between machine and ribbon isn't merely functional; it's an aesthetic partnership that defines the typewriter's overall character.
Many restorers are now actively seeking out or even attempting to reproduce original ribbon colors. This is a challenging undertaking, requiring a deep understanding of dye chemistry and a willingness to experiment. The goal isn't simply to match the color; it's to capture the texture, the feel, and the subtle nuances of the original ribbon. The intricacies of this process and the technical knowledge required underscores how much has been lost, a topic explored further in understanding the decline of silk ribbon production. Understanding how these colours came to be is the first step in recreating them, which is itself a form of historical preservation.
The Legacy of a Lost Art
The story of antique typewriter ribbons is a poignant reminder of the ephemeral nature of beauty and the importance of preserving the details that often go unnoticed. These fragile fragments of the past offer a glimpse into a world where craftsmanship was valued, and even the most functional objects were imbued with a sense of artistry. The variations in manufacturing processes that contributed to the uniqueness of these ribbons are fascinating to consider, and help illustrate the delicate balance between art and industry - a subject discussed in more detail in examining ribbon material and its implied legacy. The aesthetic considerations in placement of ribbon spacing are not to be overlooked; these elements can significantly alter the overall impression and visual resonance of the writing. The deliberate changes to production methods, driven by the desire for standardization, demonstrate how the quest for efficiency can inadvertently lead to a loss of character and individuality. The nuances of these manufacturing processes and their impact on the final product are crucial to appreciating the true value of these relics. The careful examination of these ribbons offers a unique window into an era defined by a commitment to artistry and meticulous detail.
