Echoes in the Weave: Decoding Variations in Ribbon Manufacturing Processes
There's a quiet magic in handling an antique typewriter ribbon. More than just a strip of ink-carrying fabric, it's a tangible connection to a bygone era – a whisper of letters sent, stories drafted, and memories captured. As typewriter collectors and restorers, we strive to preserve these objects, and understanding the nuances of their components, particularly the ribbons, is crucial. Identifying antique typewriter ribbons isn't merely about knowing the brand name; it’s about understanding the silent language of their construction – the echoes of the weaving processes that brought them into being. This guide will delve into the subtle, often overlooked, differences that reveal the hands and factories behind these essential typewriter parts.
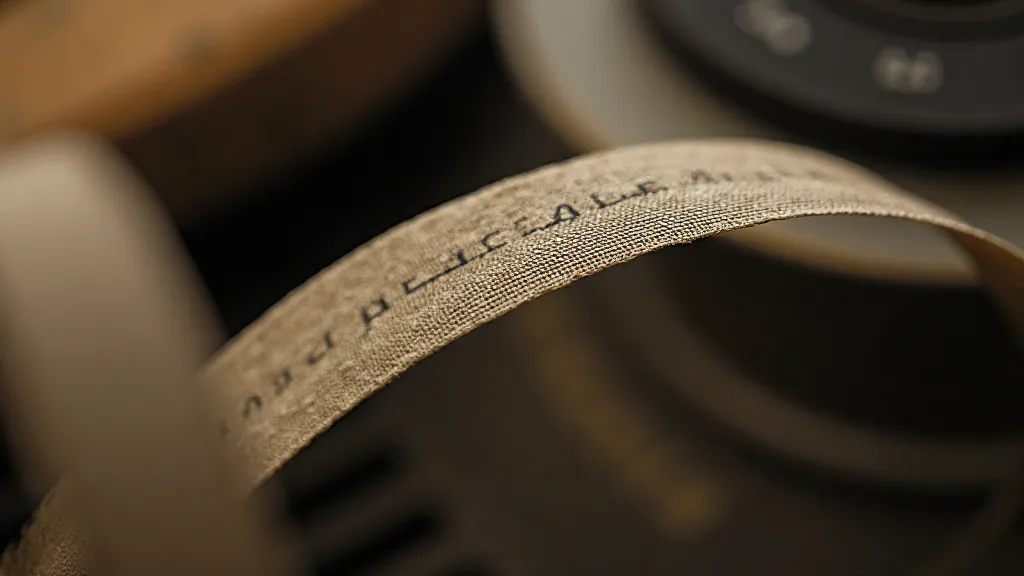
The Foundation: Materials and Early Manufacturing
Early typewriter ribbons, primarily used from the late 19th century through the mid-20th, were predominantly woven from silk. Silk's absorbency and tensile strength made it ideal for carrying the ink and withstanding the repetitive friction of the typewriter keys. Initially, production was almost entirely manual. Skilled weavers, often working in small workshops, carefully interlaced the silk threads, a process demanding immense precision and a keen eye for detail. The quality of the silk itself varied significantly – the finest ribbons used long-staple silk, prized for its strength and luster, while cheaper ribbons employed shorter, coarser fibers. The challenges in preserving these early ribbons, with their delicate construction, are significant and highlight the fragility of our tangible connections to the past.
As the typewriter’s popularity surged, the demand for ribbons outstripped the capacity of manual production. This spurred the introduction of mechanized weaving techniques. However, early mechanical looms still couldn't replicate the consistency and finesse of hand-woven ribbons entirely. This explains why even ribbons from the same manufacturer, produced in close succession, can display noticeable differences in texture, density, and overall quality. Examining the faint traces of original color, and understanding how time has altered it, truly is an exploration of ghostly echoes ribbon history.
Decoding Color Variations: Beyond the Brand Name
While brand names – Underwood, Smith Corona, Royal – are the first clues, a deeper examination of the ribbon’s color is critical. Ribbons weren’t always uniformly dyed. Variations in dye batches, the quality of the dye itself, and even the drying process can create subtle, yet telling, color differences. For example, a ribbon purported to be "black" might exhibit a faint bluish or greenish tint, indicative of a particular dye lot. Similarly, "red" ribbons can range from a vibrant scarlet to a muted brick tone. The painstaking work involved in determining a ribbon’s original color can be demanding, requiring careful consideration of the effects of oxidation and age.
Furthermore, the aging process itself dramatically alters ribbon color. Exposure to light and air causes oxidation, leading to fading and discoloration. A ribbon originally a rich purple might now appear dusty and grey. Restorers must factor in these age-related changes when trying to determine the ribbon's original hue. It’s a detective’s game of elimination, meticulously comparing the ribbon's current appearance to historical records and known examples from the same typewriter model. Preserving these fragile artifacts necessitates a profound understanding of the archivist’s dilemma ribbon preservation, ensuring they’re protected for future generations.
The Texture Tells a Tale: Identifying Loom Construction
Beyond color, the ribbon's texture provides invaluable information. Hand-woven ribbons typically display a subtle, almost organic texture, with slight variations in thread density and weave pattern. Early mechanical looms often produced ribbons with a more uniform, tightly woven structure. However, as technology improved, manufacturers experimented with different loom settings to mimic the appearance of hand-woven ribbons.
Look closely. Can you detect a subtle bias – a slight slant to the weave? This can indicate the direction of the loom’s movement during the weaving process. The density of the weave – how tightly the threads are packed together – also reveals clues. A loosely woven ribbon will feel softer and more pliable, while a tightly woven ribbon will feel stiffer and more durable. Even subtle differences in the thread thickness can be observed with magnification.
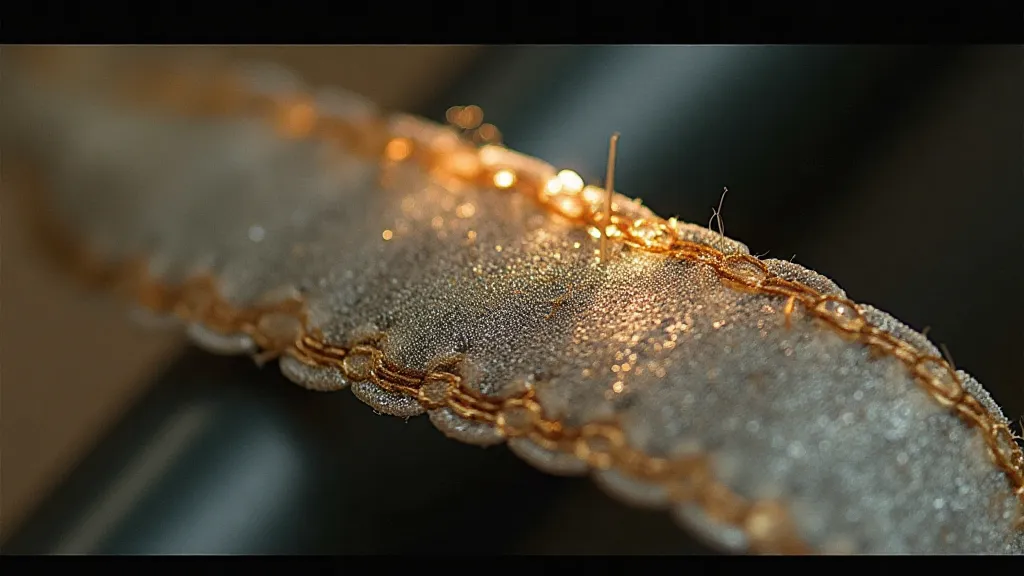
Manufacturer-Specific Signatures: Spotting the Details
Certain manufacturers developed distinct manufacturing signatures, subtle nuances in their ribbons that distinguish them from competitors. For instance, some ribbons produced by the Smith Corona factory exhibited a characteristic “crispness” to the weave – a slight stiffness that set them apart from other brands. Royal ribbons, known for their high quality, often featured a noticeably smoother texture and a consistently uniform dye.
Understanding these manufacturer-specific characteristics requires extensive study and comparison. Collecting reference samples – well-documented ribbons from various manufacturers – is an invaluable resource. Sharing observations and collaborating with other collectors and restorers amplifies knowledge and refines identification skills. It's a continuous learning process, a journey of discovery driven by a deep appreciation for the craft. The relationship between the ribbon’s design and how it was actually intended to be used is often overlooked; it’s a fascinating exploration of unwritten dialogue ribbon user intent.
The Shift to Nylon and Synthetic Fibers
The mid-20th century witnessed a significant shift in typewriter ribbon manufacturing. The introduction of nylon and other synthetic fibers revolutionized the industry. Nylon ribbons were stronger, more durable, and less prone to degradation than silk ribbons. They were also easier and cheaper to produce, leading to a rapid decline in the use of silk.
The transition wasn’t abrupt. Initially, many manufacturers produced “silk-nylon blends” – ribbons that combined the desirable qualities of both materials. These blended ribbons can be challenging to identify, requiring close examination to determine the relative proportions of silk and nylon. Later, fully synthetic ribbons became the norm, and the subtleties of the manufacturing process began to diminish as mass production took precedence over craftsmanship. However, even synthetic ribbons possess identifying characteristics related to the specific manufacturing techniques employed – the width of the ribbon, the type of ink used, and the presence of any protective coatings.
Preserving the Legacy: Restoration and Archival Practices
As custodians of these historical artifacts, we bear a responsibility to preserve them for future generations. Careful handling, proper storage, and appropriate restoration techniques are essential for ensuring their longevity. Exposure to light, heat, and moisture can accelerate degradation, so ribbons should be stored in a cool, dark, and dry environment.
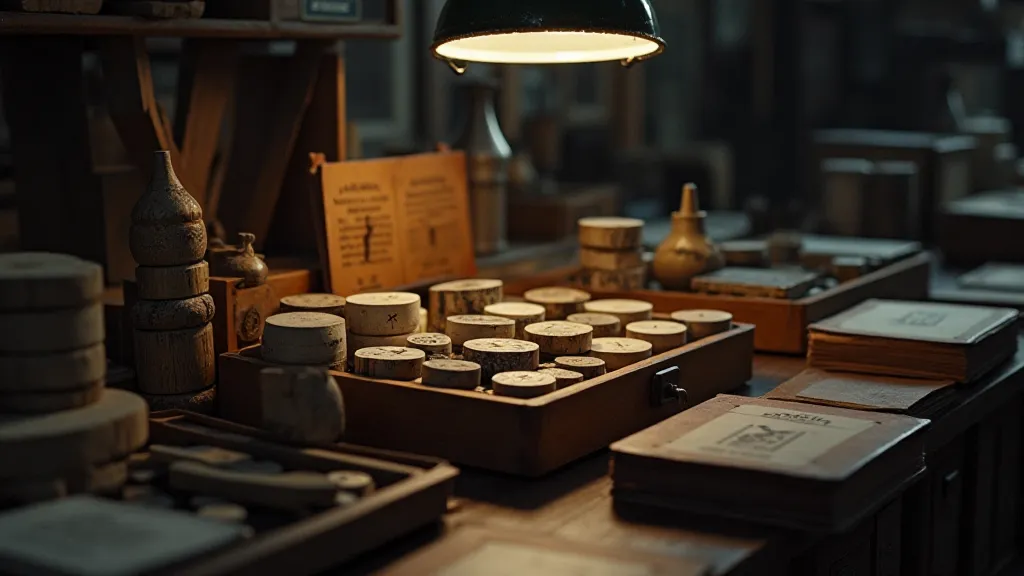
When restoring a ribbon, resist the temptation to over-clean or alter its original appearance. The goal is to stabilize its condition, not to create a “perfect” replica. Understanding the ribbon's history – its manufacturing process, its usage, and its degradation – informs the restoration approach and ensures that the intervention is both effective and respectful of its heritage. Each ribbon tells a story; our role is to ensure that it continues to be heard. The sheer variety of colors originally available, and the nuances of their creation, offers a beautiful panorama of bygone creativity – a vivid exploration of chromatic cartography ribbon palette.
The journey of identifying antique typewriter ribbons is more than just a technical exercise; it’s a window into a bygone era of craftsmanship, innovation, and human endeavor. By appreciating the echoes in the weave, we not only deepen our understanding of these essential typewriter parts, but also cultivate a profound respect for the skills and artistry that brought them into being.